How to Perform an Effective EHS Risk Assessment for Risk Management
EHS has three core pillars — Environment, Health, and Safety — and management of all three aspects is anything but simple.
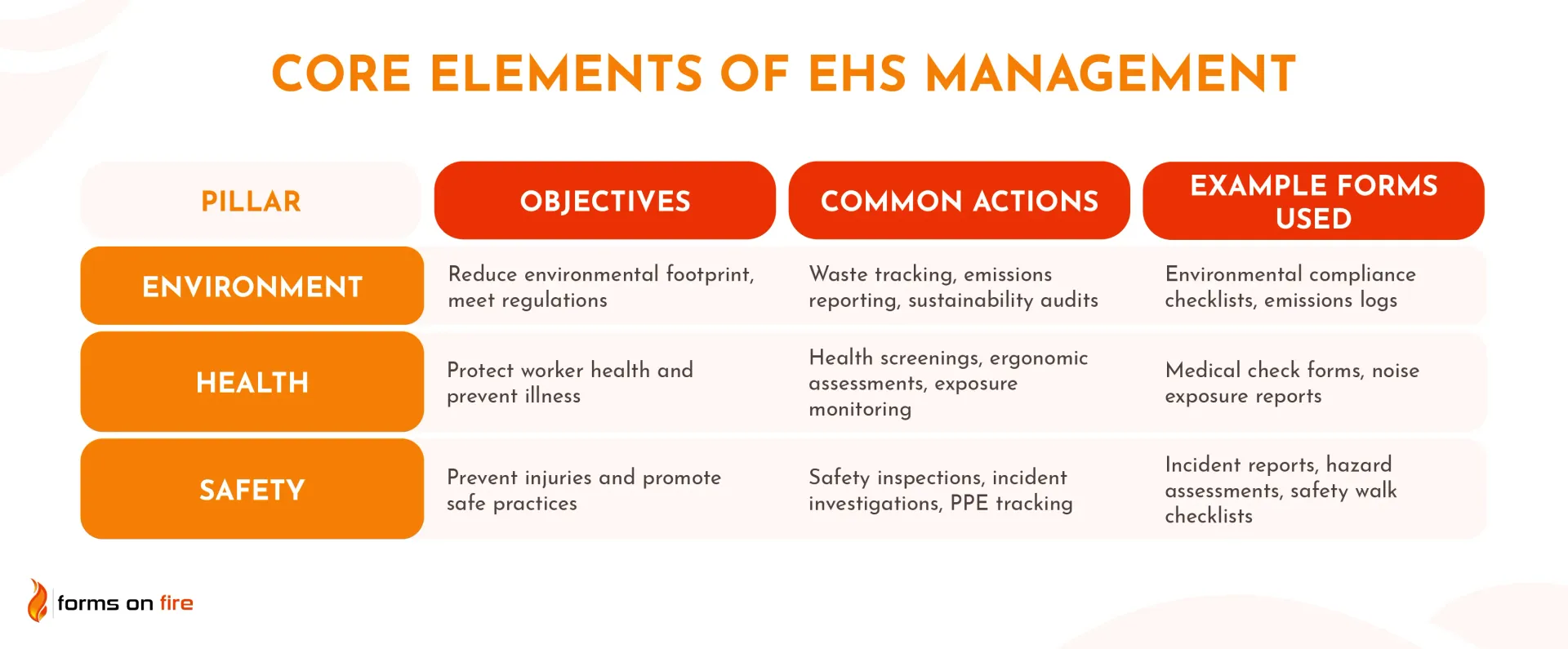
How do you keep your operations compliant, your people safe, and your environmental impact in check — all at the same time? That’s where EHS risk management comes in. It's not about reacting to incidents. It's about asking the right questions up front:
- What could go wrong here?
- How bad could it be?
- And what are we doing to prevent it?
That’s the role of a solid risk assessment. It helps you cut through the noise, prioritize real risks, and put the right controls in place, without drowning in paperwork or guesswork.
In this post, we’ll break down how to run an effective and efficient EHS risk assessment. You’ll get practical tips you can start using immediately, and see how tools like Forms On Fire make the whole process so much easier to manage.
The role of EHS assessment in the EHS risk management process
Risk assessments aren’t just a formality — they’re how you stay ahead of injuries, environmental incidents, and operational disruptions. In an EHS context, a risk assessment is your method for identifying potential hazards, understanding their impact, and deciding when and how to control them.
It’s the foundation of any serious EHS program. When done right, it feeds directly into smarter decisions, safer processes, and better compliance.
A proper assessment isn’t complicated, but it does need structure. At its core, you’re doing three things:
- Hazard identification: Look at your work areas, equipment, processes, and substances. What could go wrong? What could cause harm? You're spotting everything from chemical exposures to trip hazards to confined space risks.
- Risk analysis: Once hazards are identified, analyze how likely they are to happen and how severe the consequences would be. This could be a quick scoring method or a more detailed look, depending on the risk.
- Risk evaluation: Not all risks are equal. Here’s where you prioritize. What needs to be addressed right now, and what can be monitored? This helps focus resources where they’ll actually make a difference.
Miss any of these steps, and you’re guessing instead of managing. There’s more than common sense driving this. Regulations and international standards expect you to take risks seriously and document them properly:
- OSHA requires employers to identify and eliminate recognized hazards that can cause harm.
- ISO 45001 (Occupational Health and Safety) makes risk-based thinking part of the entire safety management system.
- ISO 14001 (Environmental Management) does the same for environmental risks — everything from spills to emissions.
But even when compliance isn’t on the line, the need for solid assessments is growing. Many organizations are moving from reactive to proactive EHS programs. And risk assessments are a big part of that shift — they’re how you stop relying on incident reports to uncover problems.
Steps for conducting an EHS risk assessment
So, how do you carry out a risk assessment that actually leads to better safety outcomes? It comes down to four key steps.
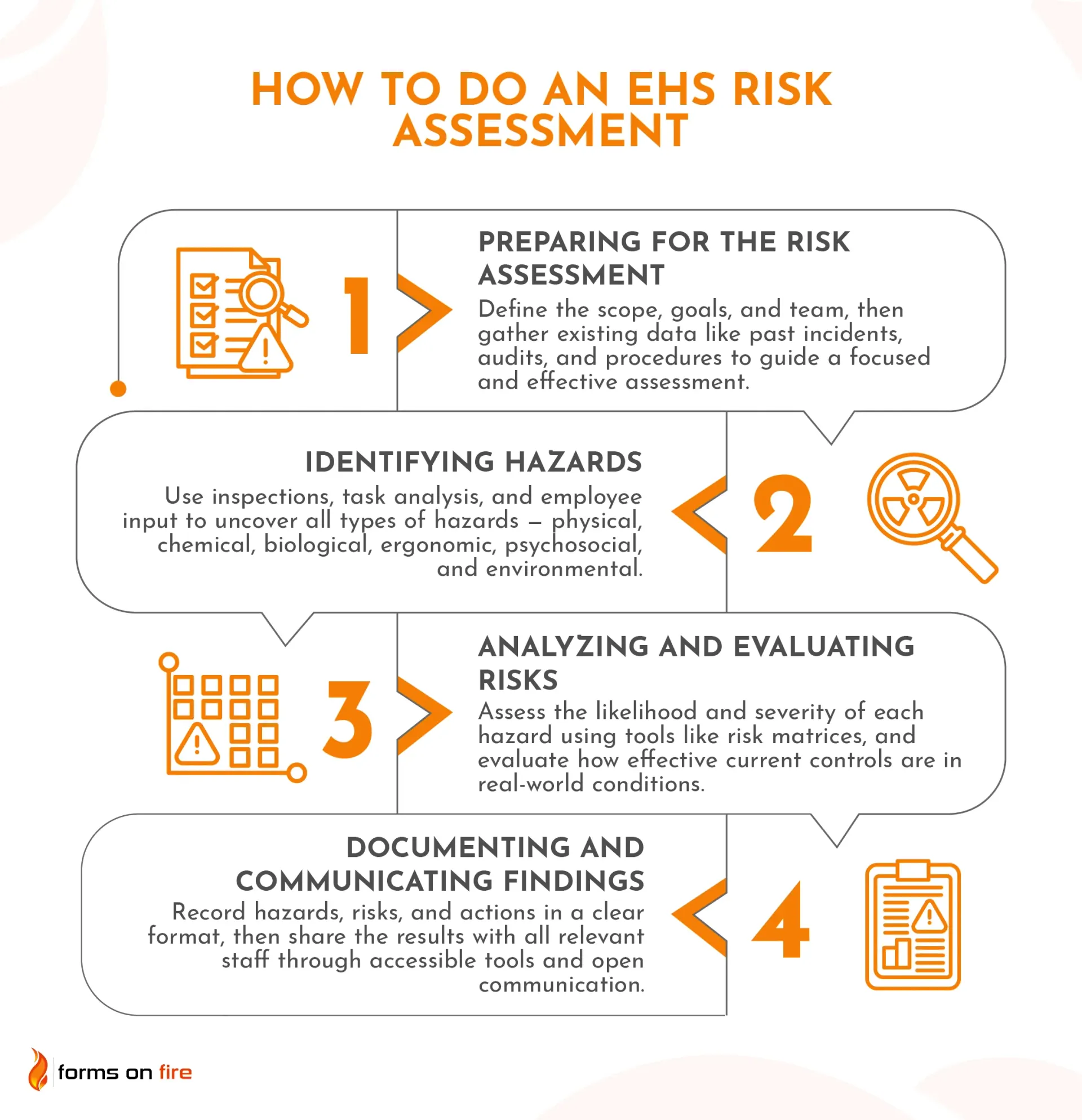
1. Preparing for the risk assessment
Start by defining what you’re assessing and why. Are you focused on a specific process? A new piece of equipment? A whole facility? Clarity here avoids scope creep and ensures you're not missing the forest for the trees.
Also, align with the goal. Is this a routine check, a response to a recent incident, or part of a broader safety initiative? The “why” will shape how deep you go and who needs to be involved.
Internal risk assessments aren’t solo work. Pull in a small, capable team with varied perspectives:
- Someone who knows the process inside out
- Someone with EHS knowledge
- A supervisor or manager with decision-making authority
- Optional but valuable: a fresh set of eyes (someone from another department).
Everyone should understand the goal of the assessment and how their input fits in. Competence matters — this isn't just about filling seats.
Before you step onto the floor, collect what’s already known:
- Past incidents: Any near-miss reports or recorded injuries related to the task or area?
- Past audits: A recent safety audit or EHS audit can tell you a lot about the current state of safety at your organization.
- Legal requirements: Know your obligations (OSHA regs, environmental limits, PPE standards, etc.).
- Work procedures: Review SOPs and job safety analyses. Do they reflect current practice or need to be updated?
This desk work may feel dry, but it saves time later and helps you ask smarter questions in the field.
2. Identifying hazards
This is the heart of the assessment. The goal here is simple: uncover anything that could cause harm — before it does. Use a mix of methods to make sure nothing slips through the cracks:
- Workplace inspections and audits: Walk the area with open eyes and a workplace safety checklist. Look at tools, machines, housekeeping, signage, and how work is actually being done.
- Task analysis: Break down each job into steps and examine what could go wrong at each stage.
- Employee input: Your frontline workers are hazard-spotting gold. They know where shortcuts happen, where things jam, and what “almost went bad” last week.
Hazards come in more flavors than most people expect. You’re not just looking for broken ladders or leaking drums. A complete assessment should cover physical, chemical, biological, ergonomic, psychosocial, and environmental hazards.
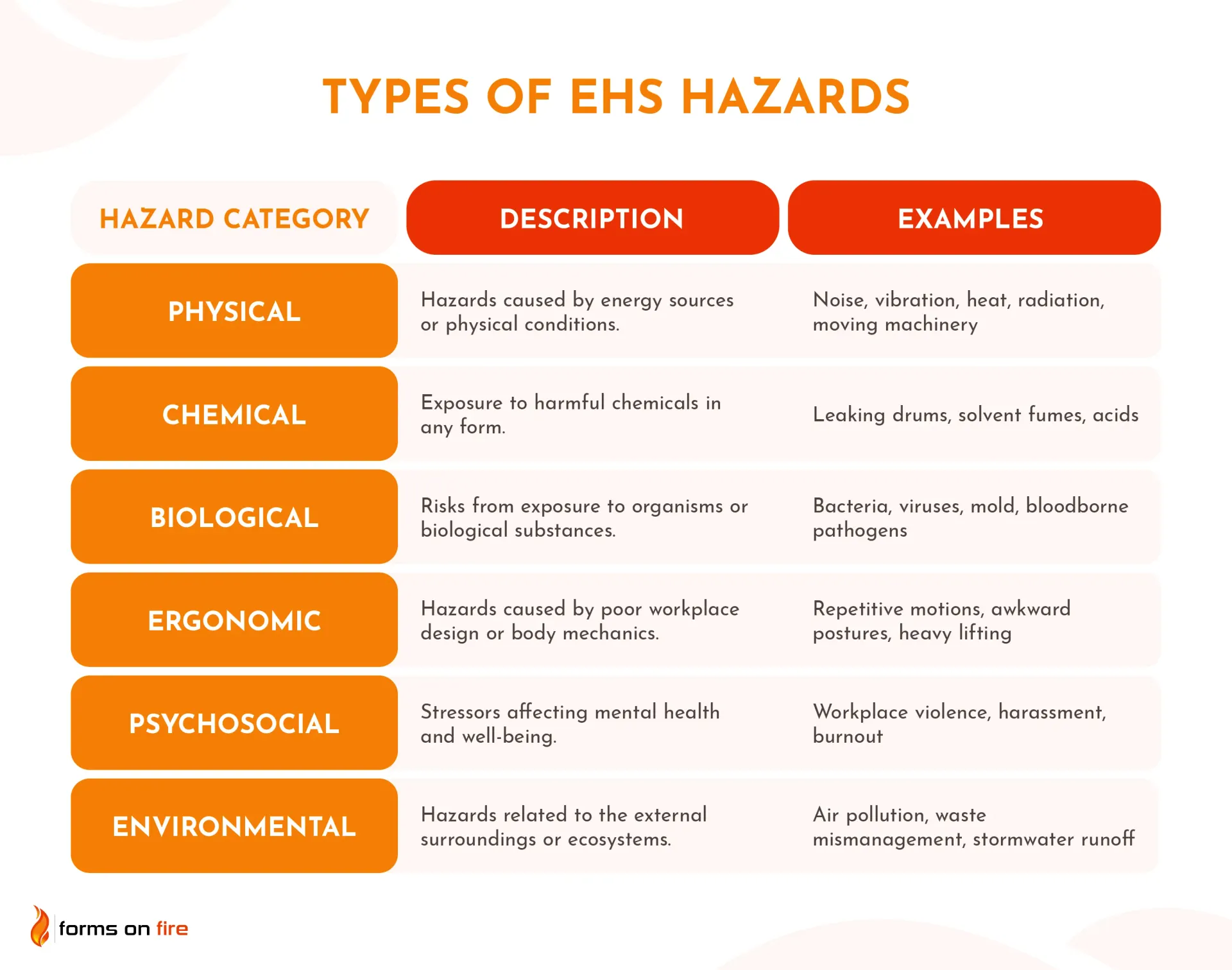
The trick is to look beyond the obvious and dig into how people, equipment, and the environment interact. You don’t need to start from scratch. These tools streamline the process:
- Digital checklists and forms: Use mobile tools like Forms On Fire to standardize inspections and log hazards over time.
- Risk assessment templates: Pre-built frameworks keep you organized and consistent.
- Job Safety Analysis (JSA): Also known as Job Hazard Analysis, this method is particularly effective for drilling down into high-risk tasks.
- Hazard and Operability Study (HAZOP): Ideal for complex systems where process deviations could lead to harm.
- Other structured methods: Like What-If Analysis, Failure Modes and Effects Analysis (FMEA), or bowtie diagrams for visualizing cause and effect.
Choose tools based on the complexity of the task and the maturity of your EHS program.
3. Analyzing and evaluating risks
Once hazards are identified, it’s time to dig into the details. Risk analysis means asking two key questions:
- How likely is this to happen?
- If it does, how bad will it be?
Some teams stick with qualitative methods — using words like “low,” “medium,” or “high” to describe likelihood and severity. Others take a more quantitative approach, assigning numbers or using formulas to estimate risk levels. Both are valid, depending on the size and complexity of your organization. What matters most is consistency and using a method your team understands and trusts.
A common and practical tool is the risk matrix. You cross-reference likelihood and severity to get a risk rating. This makes it easy to prioritize what needs attention first. Risks that fall in the high-severity, high-likelihood zone? Those are your red flags. Tackle them before anything else.
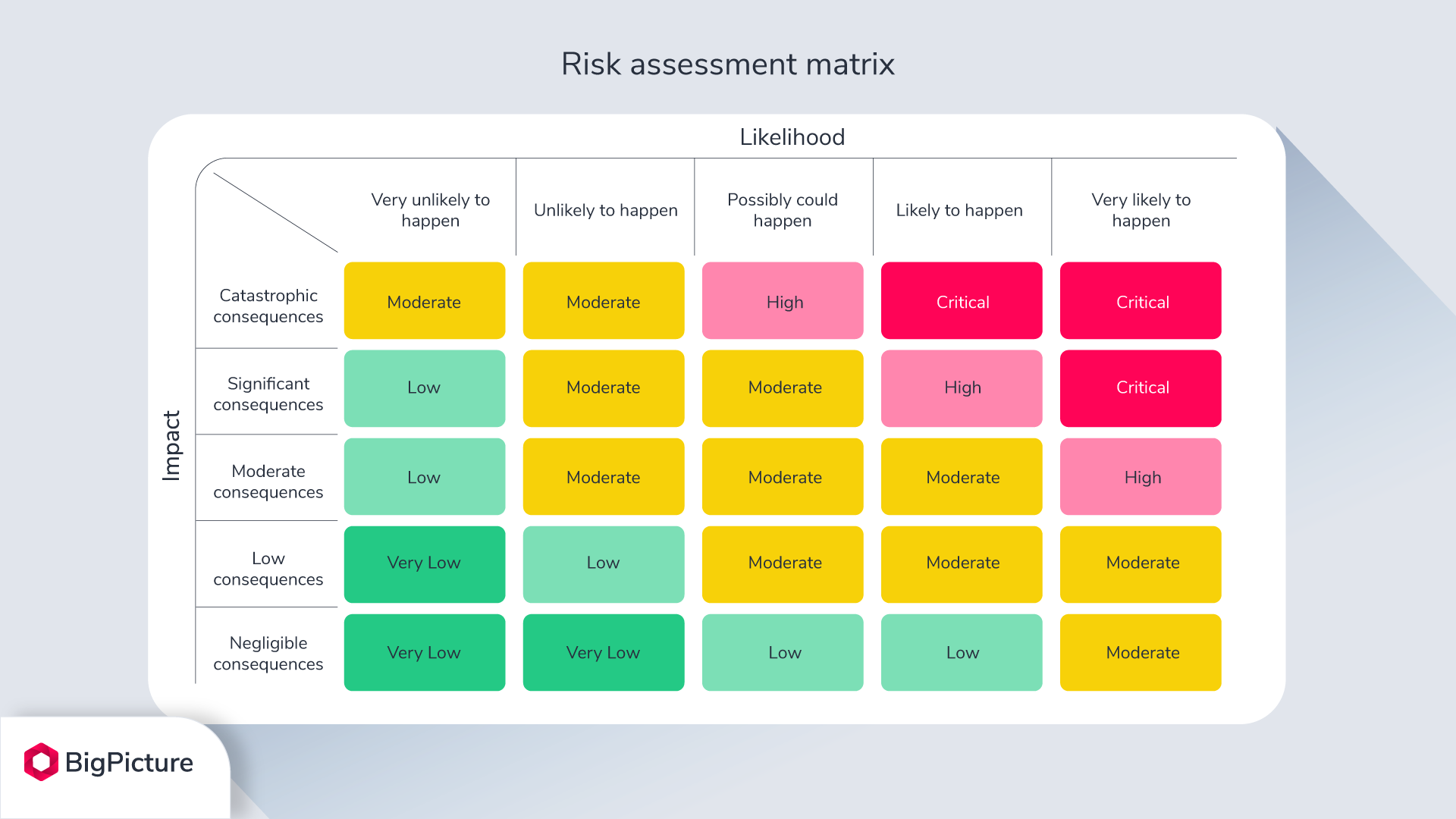
As you analyze each hazard, don’t forget to consider what controls are already in place — and how well they actually work. It’s one thing to have a guard on a machine. It’s another if workers routinely bypass it or if it’s constantly out of alignment.
Key factors to look at when evaluating existing controls:
- Effectiveness: Is it actually reducing the risk in practice, not just on paper?
- Reliability: Does it work every time, or just when someone remembers?
- Human behavior: Are people following the procedure, or working around it?
This step helps you separate low-risk items that can be monitored from those that need immediate action.
4. Documenting and communicating assessment findings
Even the best risk assessment won’t help if the findings live in someone’s notebook or get buried in a spreadsheet. Documentation is how you turn analysis into action — and prove you’ve done the work.
Every risk you identify should be recorded clearly, along with:
- The associated hazard
- The risk level
- Existing controls
- Any additional measures needed
Use a risk register or a digital platform like Forms On Fire to keep it all organized and accessible. Going digital makes it easier to track progress, update statuses, and pull up historical data — especially useful during audits or after an incident.
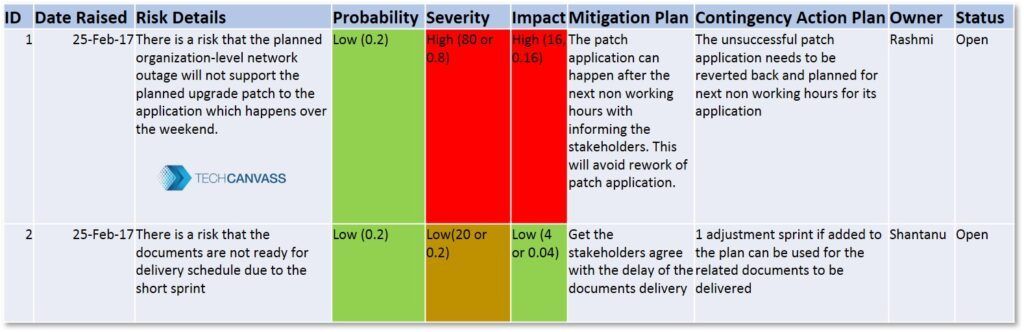
Just as important as recording the findings is making sure the right people see them. Communication shouldn’t stop at management. Workers need to know which hazards affect them, what’s being done, and what their role is in the solution.
Use toolbox talks, safety briefings, or visual dashboards to share key points. Keep it simple, relevant, and two-way — encourage questions and feedback. When documentation is clear and communication is strong, your risk assessment becomes part of how your team works smarter and safer every day.
Using EHS assessments to implement risk controls
Identifying and evaluating risks is only half the job — implementing controls is where EHS risk management becomes tangible. This is how you reduce or remove hazards, protect your team, and prevent incidents before they happen.
The best way to approach controls is through the Hierarchy of Controls, a widely accepted framework that prioritizes methods based on effectiveness:
- Elimination: Physically remove the hazard. For example, eliminate the use of a hazardous chemical by switching to a safer process.
- Substitution: Replace the hazard with something less dangerous. For example, use a water-based solvent instead of a flammable one.
- Engineering controls: Isolate people from the hazard. For instance, install machine guards or local exhaust ventilation systems.
- Administrative controls: Change how people work. For example, rotate shifts to reduce repetitive strain or add safety signage and training.
- Personal Protective Equipment (PPE): Provide gear to reduce exposure. Gloves, respirators, and hearing protection should be your last line of defense, not your first. Use them when risks can’t be eliminated through design or process changes.
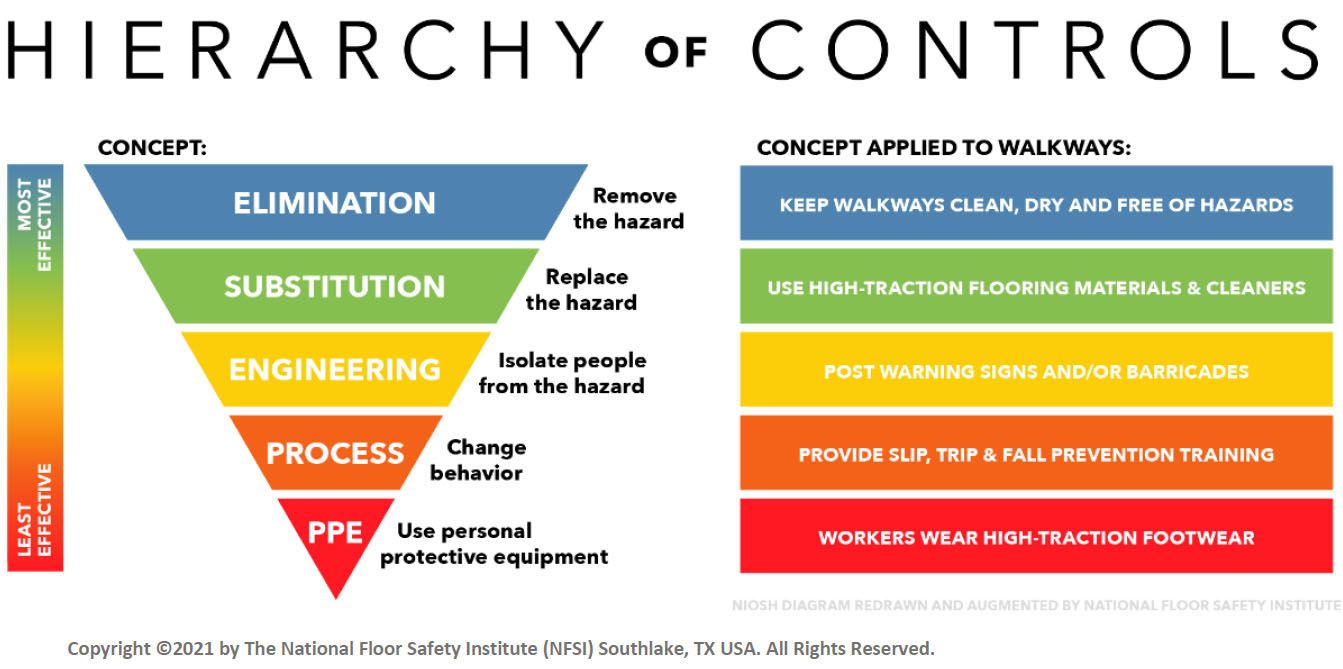
Once you’ve selected appropriate controls, they need to be built into daily operations. That means updating standard operating procedures (SOPs), modifying training, and aligning supervision. Controls aren’t helpful if no one knows about them or they don’t align with how work is done.
Assign clear responsibilities for implementing each control and set deadlines.
Vague action items like “improve ventilation” don’t drive change. But “Facilities team to install fume hood in Lab 3 by August 15” gets results.
Controls are only as strong as their follow-through. That’s why good risk assessments always end with a clear plan and someone accountable for making it happen.
Simplify EHS risk assessments with Forms On Fire
Effective risk assessments are the foundation of a proactive EHS management system. When done right, they help you get ahead of incidents, reduce liability, and build a safer workplace. But to make them consistent, scalable, and easy to act on, you need the right tools.
Forms On Fire gives EHS teams a smarter way to manage the entire assessment process. From mobile-friendly inspection forms to customizable risk registers, the platform helps you standardize your workflow, capture data in the field, and track actions in real time — all without the paperwork pile-up.
Visit Forms On Fire EHS solutions to learn how you can simplify your EHS risk assessments and build a stronger safety program. Whether you’re assessing a single task or auditing an entire site, digital forms and apps will make the process easier and more reliable.